I have passionately dedicated my efforts to several projects, investing my time in researching and prototyping. Spanning from bearing performance analysis to the intricate designs of unmanned aerial systems, these endeavors exemplify a selection of the most captivating projects I have undertaken as a member of a dynamic student team and as an engineering student.
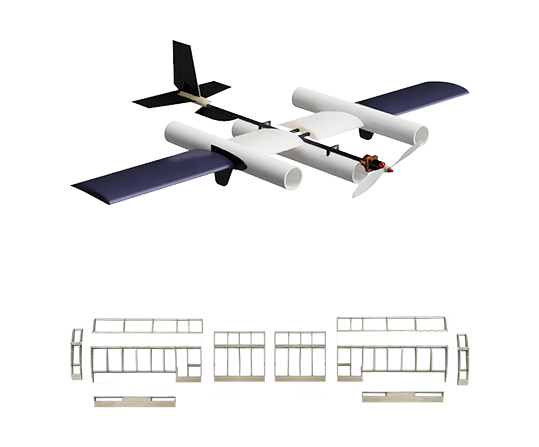
Micro-Class Unmanned Aerial Vehicle
A Micro Class Unmanned Aerial Vehicle (UAV) designed for Society of Automotive Engineers (SAE) collegiate design competition. With swift deployment from a small container in under 90 seconds, capable of carrying payloads three times its weight, this UAV finished 5th overall and 5th in flight performance in the 2019 competition.
The design includes strong carbon fiber elements for the structure, lightweight materials for the wings, and essential electronics like a brushless DC motor, nano-tech lithium-ion battery, electronic speed controller, battery eliminator circuit, and high-torque servo motors.
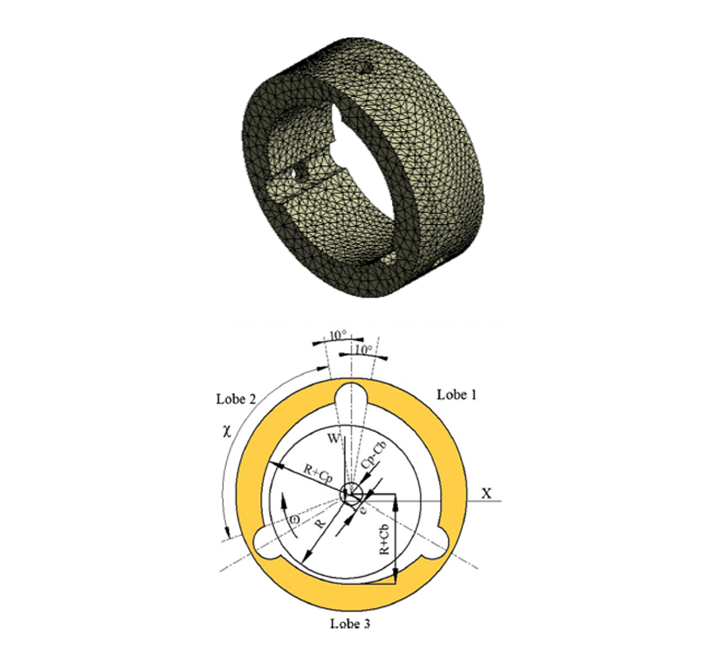
Lobe Bearing Performance Analysis
The research involved a comprehensive exploration of three-lobe bearings, focusing on hydrodynamic pressure, deformation, and stress distribution. The primary aim was to compare different combinations of eccentricity ratios and materials.
Employing a two-phase Computational Fluid Dynamics (CFD) approach and two-way Fluid Structure Interaction (FSI) with consideration for cavitation, the study utilized system coupling between static structural and fluent modules in Ansys Workbench. A database comprising of 24 distinct bearing combinations was developed. Pressure, deformation, and stress exhibit a direct correlation with eccentricity ratio increments. Further, steel displayed superior resilience compared to bronze and brass, demonstrating lower levels of deformation and stress.
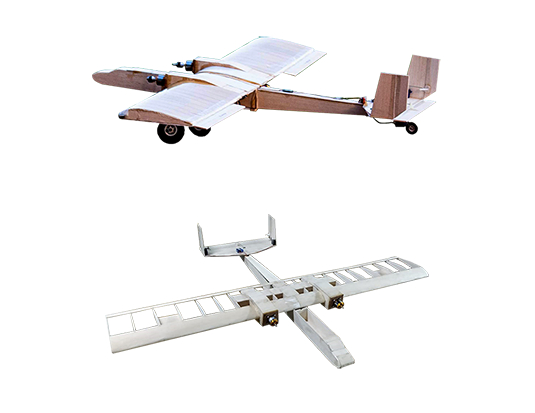
Twin-Tail Dual-Motor UAV
The Twin-Tail Dual-Motor UAV project showcases a meticulously designed aircraft with a focus on employing a dual-motor and twin vertical stabilizer configuration. This arrangement aims to enhance flight stability by preventing slipping and skidding.
The structural composition incorporates strategic motor and stabilizer placements. The electronic system encompasses essential components such as a 4S lithium-ion battery, two high RPM brushless DC motors, five high-torque analogue servo motors, and dual electronic speed controllers with integrated battery eliminator circuits. The construction materials include balsa for the fuselage, wing skeleton, and tail, plywood in areas subjected to high stress, and depron for wing sheeting.
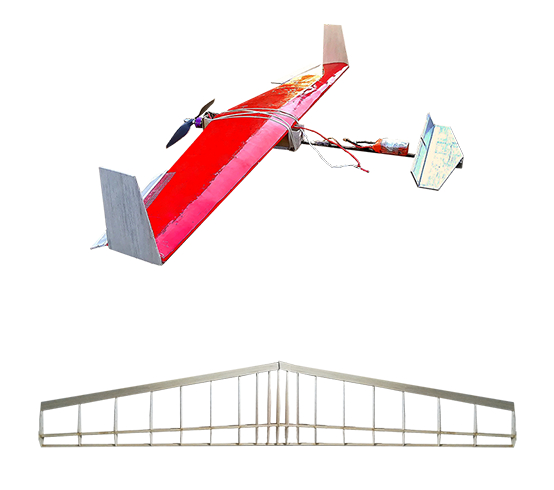
Canard UAV
The Canard UAV project is dedicated to showcasing and analyzing the canard configuration in aircraft design.
The structural blueprint involves a tapered wing design with integrated endplates, reinforced by carbon fiber composite rods to support the canard setup. The electronic components feature a 4S lithium-ion battery, a high RPM brushless DC motor, an electronic speed controller with an integrated battery eliminator circuit, and three high-torque analogue servo motors.
The construction materials incorporate balsa for the fuselage, wing skeleton, and canard, plywood in high-stress regions, and lightweight plastic shrink wrap monokote film for wing sheeting. This project provides valuable insights into the dynamics and benefits of utilizing the canard configuration while employing a well-considered mix of materials for optimal performance.
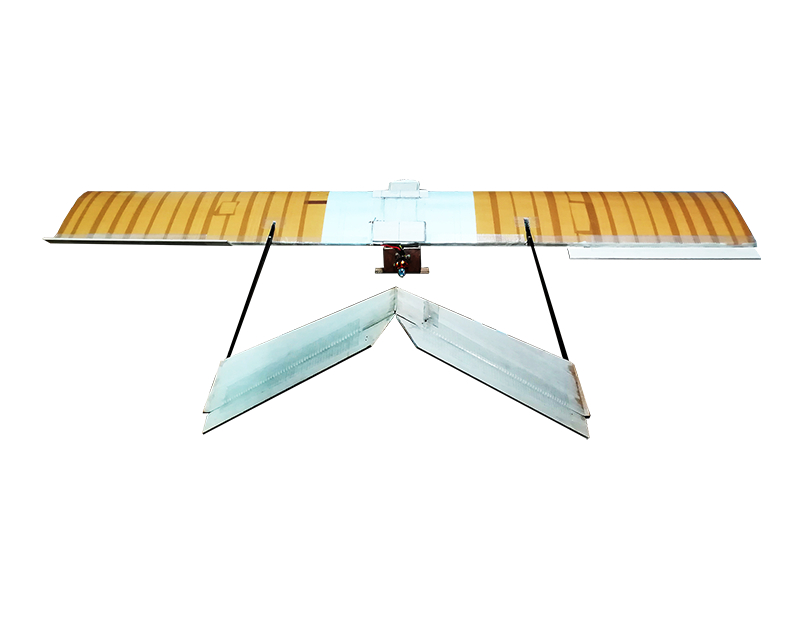
A-Tail UAV
The A-Tail UAV project is designed with the aim of showcasing and analyzing the A-Tail empennage configuration.
The structural layout features a conventional wing design supported by two carbon fiber reinforced composite rods that facilitate the A-Tail configuration. The electronic system comprises a 4S lithium-ion battery, an electronic speed controller with an integrated battery eliminator circuit, high RPM brushless DC motors, and four high-torque analogue servo motors. The construction materials thoughtfully incorporate balsa for the fuselage, wing skeleton, and tail, plywood in high-stress regions, and depron for wing sheeting. This project offers valuable insights into the dynamics and advantages of employing the A-Tail empennage configuration.